HIPERPAV’s uses to the pavement and construction industries are extensive. HIPERPAV is designed to improve pavement performance and durability through the careful selection of input parameters related to concrete materials, pavement design, pavement construction, and climatic conditions. This synergistic approach to concrete pavement design yields many applications:
- HIPERPAV can be used to predict and prevent uncontrolled cracking in jointed concrete pavements at early ages. The temperature and moisture models contained in HIPERPAV predict the development of the pavement’s concrete strength, as well as the pavement stresses. As long as the stresses are lower than the strength of the concrete, cracks are not likely to occur. If cracking is possible, HIPERPAV allows the user to modify input parameters and to tailor the design and construction to minimize the possibility of crack formation.
- HIPERPAV can be used to determine the optimum joint sawcutting window during construction. When sawcutting joints in concrete pavements, it is important that the joints are not sawcut too early or too late. If joints are cut too early, the strength gained by the concrete may be not enough to support the saw cutting equipment. This will cause structural damage to the pavement. Likewise, raveling along the joint can occur, which can later turn into significant spalling damage. If the joints are cut too late, uncontrolled cracking may occur at any point in the pavement. The joints need to be cut before the tensile stresses in the concrete exceed the concrete strength. This window of opportunity can be determined using HIPERPAV.
- HIPERPAV can assist in assessing the costs and benefits of opening a concrete pavement to traffic. Opening pavements after construction in a prudent and expeditious manner is needed to minimize user costs. Rehabilitation and reconstruction operations on congested streets and highways are a common source of frustration and delays for commuters. HIPERPAV can predict the time when adequate strength has developed in the concrete so that the roadway can be opened to traffic.
- HIPERPAV can quantify the risks of using stabilized bases. Stabilized bases often lead to extremely high friction stresses between the pavement and the subbase. This is a common cause of uncontrollable cracking at early ages.
- Using HIPERPAV, the stresses generated in the concrete from the interfacial restraint can be evaluated. This allows the pavement design to be modified to prevent the formation of cracks by using bond breakers at the interface.
- HIPERPAV can predict the impact of climatic conditions on pavement performance. A cold front, or paving in desert climates where there are significant temperature drops from day to night, can be evaluated in terms of pavement performance. The damage caused by these sudden climatic changes can be prevented with HIPERPAV, since it can simulate ways to prevent pavement damage. Possible alternatives are to control the temperature of the concrete mix, to select a different time for placement, or to use different curing methods.
With the incorporation of the CRCP module, many of the benefits in the original HIPERPAV system are now also applicable to this pavement system as well.
Prediction of JPCP long-term performance will assist the practitioner in optimizing the selection of design and construction factors that minimize long-term performance distress, therefore, promoting high performance concrete paving. - The incorporation of mix optimization and dowel analysis modules in HIPERPAV will open up a new door to development of a series of early-age concrete products intended to promote better design and construction of concrete pavements. This will improve long-term pavement performance and reduce the costs of pavement rehabilitation in the long term.
Given its wide range of applications, HIPERPAV is currently being used as a tool by planners, designers, and contractors. During the planning stage, HIPERPAV is used to develop quality control specifications for a particular project based on the available materials and climatic conditions of the region in study. Designers use HIPERPAV to optimize their pavement designs based on the best selection of the design variables. This will produce a better end product and guaranteed long-term pavement performance, while maximizing economy.
Contractors use HIPERPAV to prevent expensive repairs by predicting potential damage due to unexpected conditions and determine the best set of factors that will prevent damage to the pavement. Finally, the software is used in pavement forensic studies to assess the causes of pavement damage and poor pavement performance.
HIPERPAV is used by contractors for various reasons:
- As a forensics tool, to determine if outside conditions are favorable for paving activities
- For quality control
- To schedule sawcutting activities
HIPERPAV has been used by state agencies and contractors to help them develop high quality concrete that will provide exceptional performance over the life of the pavement. HIPERPAV has been used to:
- Determine how the weather can affect pavement performance,
- Predict and prevent uncontrolled cracking in jointed concrete pavements at early ages,
- Determine the optimum joint sawcutting window during construction,
- Determine how early the pavement can be opened to traffic,
- Predict the pavement performance using stabilized bases, and
Optimize concrete mixes.
Case Studies
Cement Type
Cold Front Scenario
Coefficient of Thermal Expansion
Mid-Panel Cracking
Sawcutting Schedule
Faulting
Time of Placement
Aggregate Selection
Temperature Fluctuation
HIPERPAV can be used to minimize early-age PCCP cracking. In the following cost benefit analysis, the cost of ½ % early-age PCC cracking is evaluated for a typical paving day and the numbers computed are scaled up nationally to show yearly potential savings with the use of HIPERPAV.
The following costs were provided by a paving contractor in the Midwest:
- Typical cost of new PCCP: $30.00/sy
- Typical cost of PCCP removal and replacement: $200.00/sy
Estimating the cost of ½ % early-age cracking for a typical PCCP construction day:
- Length: 3000 ft (1000 yd)
- Paving width: 36 ft (12 yd)
- Area: 1000 * 12 = 12,000 sy
- New PCCP cost = $ 360,000/day
- Cost of cracked slabs (0.5%) = $ 1,800/day
- Remove and replace cost = $12,000/day
Estimating the cost of using HIPERPAV:
- 1 technician at $60/hr
- Time running the software: 4h per day to gather inputs, run, create and file reports
- Total cost of running HIPERPAV = $60/hr * 4 hr = $ 240/day
In summary, the cost of running the software would be $240/day with potential savings of $12,000/day at a benefit-cost ratio (BCR) of 0.98.
In reality, not every single PCCP project ends up with 0.5% cracking, some projects may successfully avoid cracking, while others may result in higher amounts of cracking. However, preventing a single crack from occurring (1 slab ~ 20 sy) can save approximately $4000 over $240/day running HIPERPAV.
Applying the above calculations for all PCCP placed in the US (estimates for 2006 based on ACPA Pavement Market Quarterly):
- PCCP Construction costs (2006 Q1-Q4): $ 2,513,210,000
- Estimated cost of cracked slabs (0.5%) = $ 12,566,050
- Estimated Cost of removal and replacement = $ 83,773,667
- Potential savings using HIPERPAV to prevent cracking = $ 82,098,193 /year (at a BCR=0.98)
It must be emphasized that this analysis does not take into account additional benefits such as reduction in project time and/or user delays due to the reduction in PCCP removal and replacement operations.
Potential savings per state are presented below:
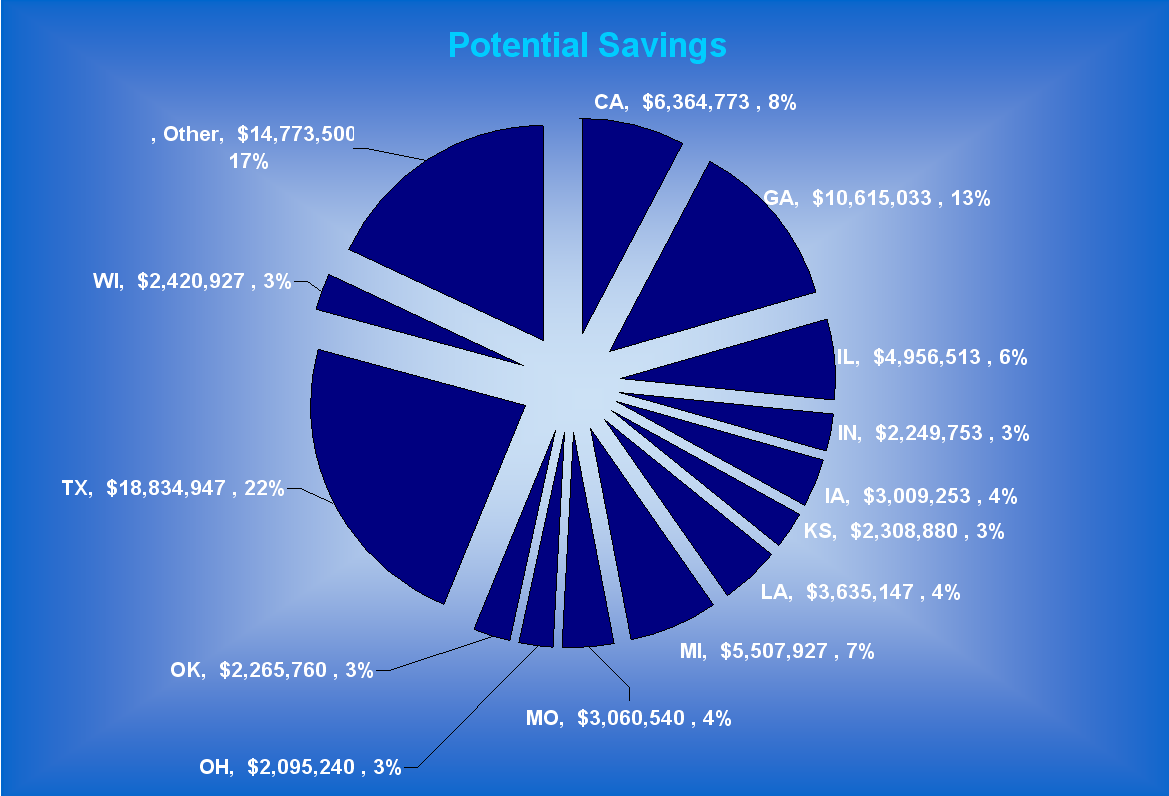
Potential Savings: Based on PCCP Construction from ACPA, Pavement Market Quarterly, Vol 8.1, Oct-Dec 2006